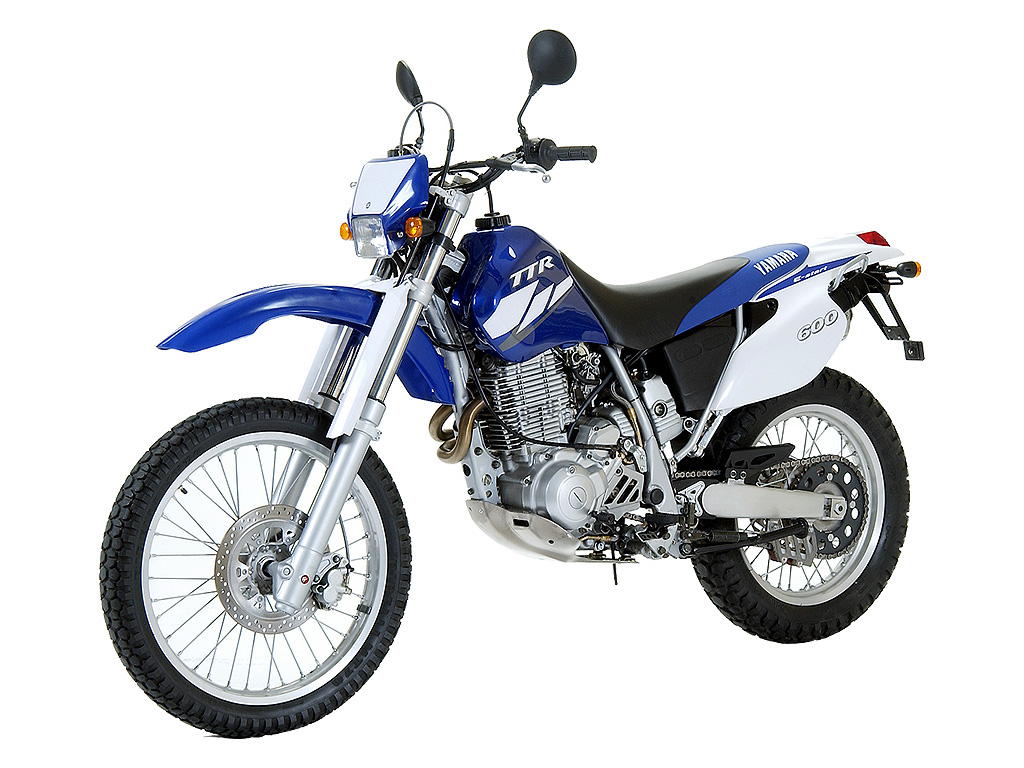
Everything posted by Airhead
-
2024 Merry Christmas and a Happy New 2025
Merry Xmas NEO 👍
-
2023 Merry Christmas and Happy NEW YEAR 24
Happy new year to you both.
-
Fork seals
how could you get the seals out with the stanchions in place?
-
1978 DT 125E forks.
Theyre not the same and neither are the dimensions, even the brake plate is different between the models so youd have to fit the complete fork plus brakeplate I think
-
Last of the Twinshocks '78 DT175
last time he was on here was 2018 Lenmac
-
DT175 Basic Wiring
there should be a red wire connecting stator and cdi. whats the question mark mean?
-
DT175 Basic Wiring
Hi Blake and welcome, is this any help? DT175MX Ignition checks There were two versions of ignition systems on DT175MX bikes. The mk1 version from the earlier bike had a 7 wire CDI the early bikes had a round section swing arm. The mk2 version had a 6 wire CDI, the red wire is absent on these. These bikes have a square section swing arm. The HT cap (AKA spark plug cap) unscrew it off the HT lead, it is supposed to be a resistor cap so should be around 5K Ohms The ignition coil primary...Orange wire to battery neg should be 1 Ohm +- 10% The ignition coil secondary...HT lead to battery neg should be 5900 Ohms +- 20% If the readings are much higher, check the ignition coil has a clean ground connection. Yes and the ignition coil mounting is a wiring harness ground point too, so check its clean and bright there. Disconnect all the wires from the CDI. Then using your multimeter on the loom side of the connectors. Black probe on a clean part of HT coil ground point Red probe on...... Orange, Meter to 200 Ohms, expect 1 Ohm (HT coil primary) Brown, Meter to 2k Ohms, expect 420 Ohms for mk1 and 300 Ohms for mk2 (Magneto charge coil) White/Red, Meter to 200 Ohms, expect 12.4 Ohms for mk1 and 10 Ohms for mk2 (Magneto pulser coil) Red, Meter to 200 Ohms, expect 13.6 Ohms for mk1 only. (Source coil 2 or high speed coil) Black female connector, Meter to 200 Ohms, expect dead short repeat for black male connector Any difference in the results for the two black wires may possibly be rectified by cleaning the front engine mounting bolt and a little of the frame behind the bolt head, then tighten to torque spec. Black/White, Meter to 20K Ohms, with ignition off expect dead short, with key on expect open circuit, with kill operated expect dead short (Engine kill operation) If all these tests are good you would be well advised to try another CDI. If they are not good...reading higher...disconnect and clean any plugs/sockets you find along the way, if the magneto coils are reading lower, new ones needed if more than 10%...or so the book says file:///C:\Users\Dell\AppData\Local\Temp\msohtmlclip1\01\clip_image001.gif Finally, if you are working with a box full of mixed parts! Mk1 1 flywheel is Mitsubishi F3T250, it has two slots in the face of the flywheel Mk2 flywheel is Mitsubishi F3T251, it has four slots in the face of the flywheel
-
Xt 600 E 3TB bitsa
Thats really nice, well done!
-
TZR 125 help needed, I'm at my wits end.
Your not likely to get a reply, he's not been back since 2012 !
-
Hi from Portsmouth and my R1-Z250
That looks like a lot of fun Alfie👍
-
Sheared cylinder nut and broken cylinder
Yes, this.
-
Sheared cylinder nut and broken cylinder
You've misunderstood me, have you pulled the threads out of the casing?
-
Sheared cylinder nut and broken cylinder
My concern is, have you pulled the stud from out of the engine case?
-
Sheared cylinder nut and broken cylinder
Bugger! Can you heat it and move it with some water pump pliers. I really can't understand how the cylinder base broke like that unless there's a fragment of old gasket involved. If the cylinder is no use any longer and it looks that way, you may have to cut the fins away for better access?
- Not a Yamaha, but
-
Starter Motor intermittent while riding
Could be water in the handlebar push button? Give it a spray of WD40 or equivalent
-
Hi everyone
Greetings ditchkid, yes that really is a proper intro, thanks. Like the bikes they're both interesting. What's the plan for the TT are you making it roadworthy?
-
Yamaha RS100 (1Y8) putting out 25V instead of 6V
See the image that Cynic posted? If yours is like this one then check the yellow wire connection and check the body is connected to ground
-
You have got to be shipping me!
no good mate, nowhere to anchor the drum brake stator, and besides he'll no douubt want to keep to standard @Scott what's wrong with your original forks?
-
DT175MX 1978 Build
That's in a poor state! What expensive tools do you think you have to buy? Try Yambits for the stator plug?
-
Cranky DT175MX...
You could put it together and test the rotor with a dti ( dial test indicator) any local engineering firm may be able to do this for you? How did it get bent?
-
Cranky DT175MX...
It's hard to tell but actually the rotor site on the tapered part so if that's not bent it might be ok?
-
Xvs125 dragstar info
There's a model code label on the frame somewhere Chris
-
1980-G DT175MX 2-Stroke Oil Leak (US Model)
Yes they are just a taper fit, if you get a grip and wiggle them they pull out
-
1980-G DT175MX 2-Stroke Oil Leak (US Model)
Yambits YBK053 Oil Pump Repair Kit. For reference the oil seals are 25mm diameter x 14mm diameter x 5mm deep (seal1) and 9mm diameter x 4mm diameter x 3mm deep (seal2)